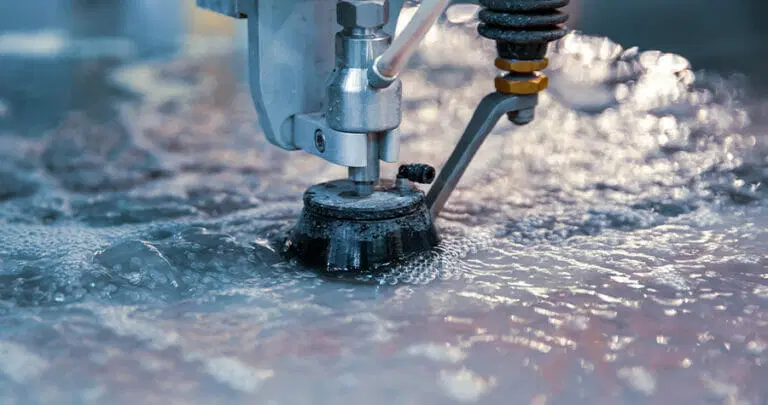
Industrial Waterjet Cutting Services (Up to 6m x 2m & 200mm Thick)
Precision Cutting for Thick and Large Metal Components
At AWP, we offer advanced waterjet cutting services capable of handling large-format sheets up to 6 meters by 2 meters and cutting through materials up to 200mm thick, including hardened steel. Our high-pressure waterjet systems deliver clean, accurate cuts without heat distortion, making them ideal for sensitive and heavy-duty applications.
Key Features of Our Waterjet Cutting Services
- Large-Format Cutting Capacity
We specialize in cutting oversized sheets and plates up to 6000mm x 2000mm, perfect for industrial and structural components. - Thick Material Cutting
Our waterjet systems can cut through up to 200mm thick steel, including stainless steel, aluminium, and specialty alloys. - Cold Cutting Process
No heat-affected zones (HAZ), preserving material integrity and eliminating warping or hardening. - High Precision & Clean Edges
CNC-controlled cutting ensures tight tolerances and smooth finishes, reducing the need for secondary processing.
Materials We Cut
- Mild Steel
- Stainless Steel
- Aluminum
- Copper & Brass
- Titanium
- Glass, Stone & Ceramics
- Composite Materials
Industries We Serve
Our waterjet cutting services are trusted by clients in:
- Oil & Gas
- Construction & Infrastructure
- Marine & Offshore
- Aerospace
- Automotive & Heavy Equipment
- Architectural & Decorative Metalwork
Why Choose AWP?
- ✅ Heavy-Duty Capability – Cut up to 200mm thick and 6m long materials with precision.
- ✅ Versatile Cutting – Suitable for metals, non-metals, and composite materials.
- ✅ No Heat Damage – Ideal for sensitive materials and high-performance applications.
- ✅ Fast Turnaround & Competitive Pricing – Efficient production and cost-effective solutions.
Request a Waterjet Cutting Quote
Need expert waterjet cutting for thick or oversized materials? Contact AWP today to discuss your project or request a custom quote.